installing vortex-reducing fins(PBCF)
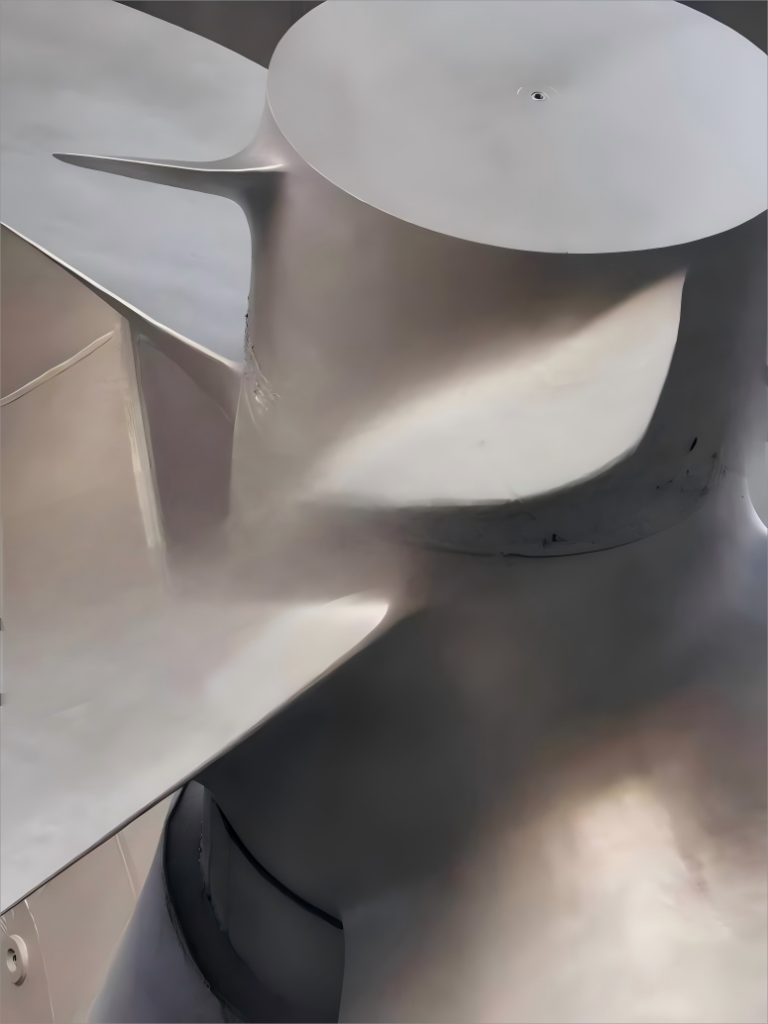
Energy-saving modification is of great significance in the modern shipping industry. In particular, with the increasingly stringent environmental regulations and the rising fuel costs, shipowners are increasingly in need of energy-saving equipment. In this context, domestic shipowners have adopted propeller boss cap fins (PBCF) as an effective means of ship energy-saving modification.
PBCF is a device installed at the rear of the propeller shaft that reduces the generation of vortices by changing the flow of water around the propeller. When the propeller rotates, vortices will form at the tail of the propeller blades, resulting in thrust loss and reduced propulsion efficiency. The main function of PBCF is to break these vortices by adding vortex-breaking fins, thereby reducing energy loss during ship propulsion.
Combined with Chief Industry Limited’s recent installation cases for domestic ship owners, we can get a more detailed understanding of some practical design and difficulties.
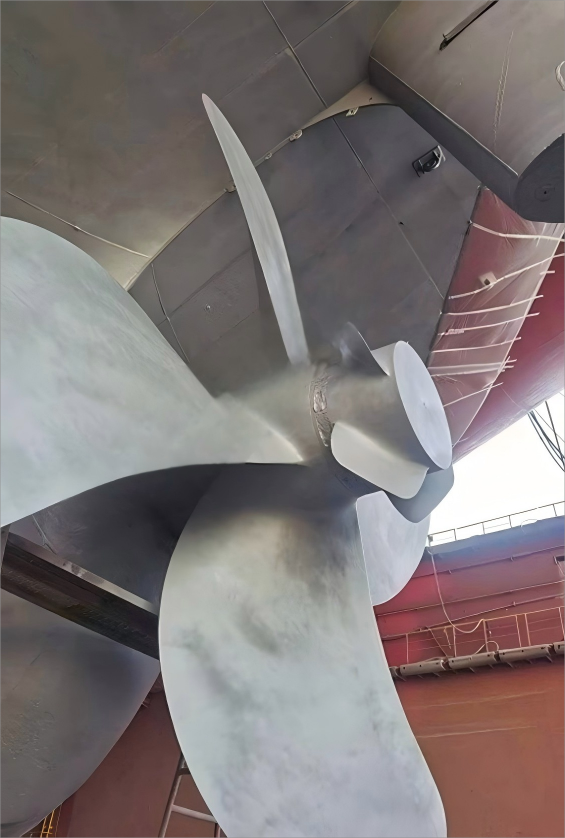
Chief industry limited ‘s PBCF project practice
We were also introduced to this project at last year’s Marinetec Shanghai. When finalizing the product shape, we drafted a design that took into account multiple factors, such as the position and pitch angle of the fins relative to the propeller, so that our PBCF could adapt to a wide variety of vessels. When the PBCF was first developed, we created a formula to determine the fin height, length and angle for various propeller types (4 to 6 blades). However, in order to determine the optimal shape, we had to generate design charts for a more precise design by using the Towing Tank Test and CFD (Computational Fluid Dynamics) analysis. We later checked it using actual ships.
What problems did you actually encounter after participating?
One feature we added to the PBCF we designed was its greater fin height than conventional models. The second feature was its streamlined configuration. While the propeller action tends to have a greater effect on the bow side of the fin, we found that there was still a lot of drag at the stern, so we focused on streamlining the stern side components. The third feature we improved was the pitch angle. We increased the twist in the fin shape by slightly changing the radial pitch.
Before our improved model was finalized, we discovered two key points through CFD analysis and our years of industry experience. First, in order to improve performance and achieve higher energy efficiency, we need to increase the height of the fins. Second, once the fins exceed a certain height, the drag starts to increase and does not produce any additional effect.
Increasing the fin height also puts more pressure on the fin root, which requires making this part thicker. This, in turn, requires the fuselage to be correspondingly thicker, which brings increasing challenges to PBCF design.
Since the PBCF is mounted at the tail of the propeller shaft, its weight affects the bending and flexing capabilities of the entire shaft. When it is too heavy, it can significantly reduce the service life of the stern shaft bearing. If the tail becomes too heavy, the entire propeller shaft system may need to be rebuilt. So, depending on the ship type, this requires more extensive design changes. Our biggest challenge is to ensure that this does not happen.
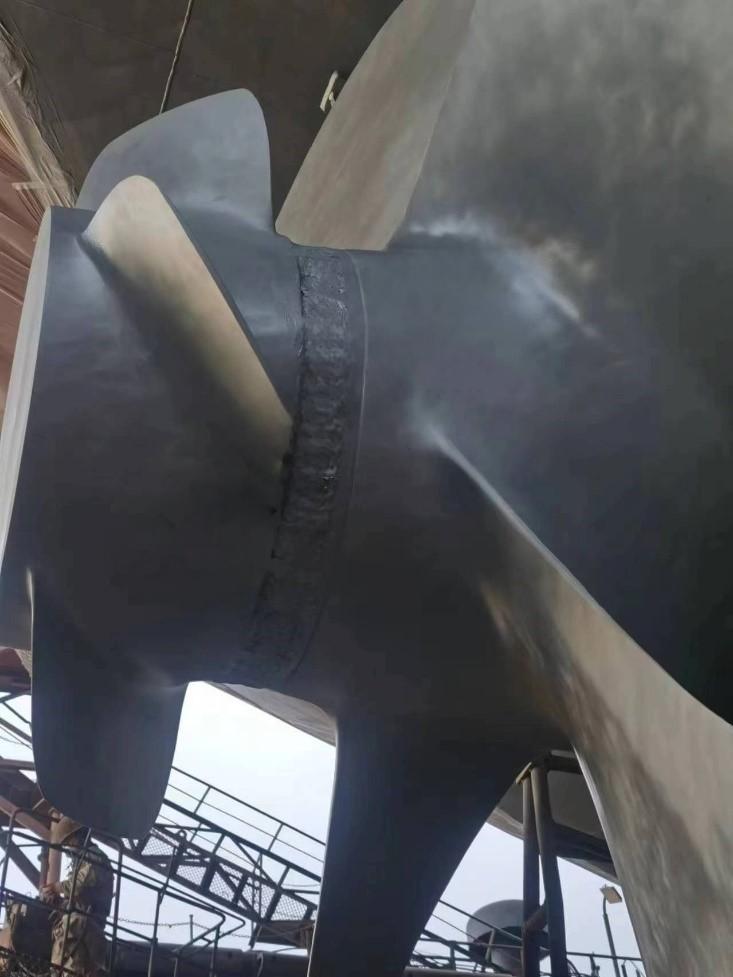
What is the feedback from most ship owners after installation?
The installation of PBCF can significantly improve the propulsion efficiency of the ship. According to research and actual ship tests, PBCF can reduce a ship’s fuel consumption by about 2% . This energy-saving effect is very significant for ships in long-term operation. Especially on ships with long sailing time and high fuel consumption, the saved fuel costs have a significant impact on the economic benefits of the operator.
If you have any needs for PBCF modification of operating ships, please contact us
JACKIE DUAN Business Support
Tel: +86 19384118340
Email : jackie@chief-industry.com